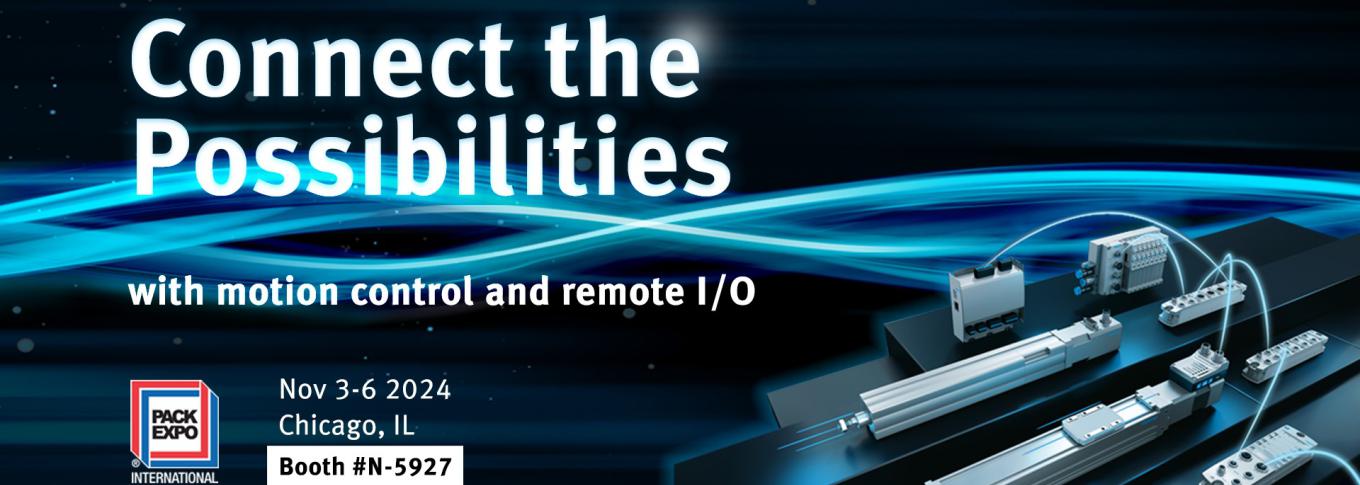
Festo Introduces at Pack Expo Its New Flagship Valve Terminal – VTUX
Festo introduces its new flagship valve terminal, the VTUX. The VTUX can serve as I/O, remote I/O, and decentralized I/O. These compact and rugged IP65/67-rated terminals can be located anywhere on a machine that boosts operational performance and original equipment manufacturer (OEM) installation productivity. VTUX modularity results in less inventory and lower overhead costs. The new VTUX is on display at the Festo Pack Expo Booth # N-5927, McCormick Place, Chicago, November 4-6.
VTUX is both compact and lightweight, an advantage for end-of-arm tooling and conserving space on a machine or in a control cabinet. The terminal is made from a high-performance polymer so rugged and durable that these units can be placed in welding cells.
The key to the VTUX’s unparalleled flexibility is its modular design. For higher flow rates, a high flow subbase is used and for space saving needs, the compact subbase. A single valve model can be used for both subbases, which simplifies ordering, stocking, and support. High flow and compact subbasses of one or four valve positions can be mixed and matched on a terminal. VTUX terminals can have up to 128 valves with up to 128 solenoid coils. The VTUX also features vacuum capability.
VTUX offers a platform for fully integrated vacuum solution for configuration of up to sixteen vacuum channels per terminal. The platform enables bidirectional communication from the PLC to the vacuum generator. Vacuum and ejector pulse can be individually controlled. VTUX vacuum delivers high vacuum or large suction volume flows and can be combined with valves. Parameters can be changed via teach-in from the PLC during operation. There is an integrated vacuum sensor for continuous monitoring of actual values and there is a parameter-based air saving function. The system monitors vacuum for early detection of faults or errors during operation.
The electronics side of the terminal offers the same flexibility as the pneumatics side by featuring mix and match modules. For example, users can add multiple analog or digital I/O modules, including I/O-Link. The modular concept continues through to the method of communication between controller and terminal. The choices include the new Festo Automation Platform (AP) for backplane speed communication in all top communication protocols. All AP-based modules appear to the control engineer to be under a single IP address, simplifying commissioning and allowing smaller and less expensive PLCs to be specified. Additional communication modules include IO-Link, AP-I for decentralized I/O, and multipin connector.
CODI Manufacturing
CODI Manufacturing, Littleton, Colorado, introduces at Pack Expo in the Festo booth a compact, flexible 12-cycle-per-minute case packer for small to mid-sized food and beverage companies that achieves an industry leading price/performance ratio.
CODI Manufacturing utilized the Festo Handling Guide Online (HGO) engineering tool to design the two-axis handling system, the core of the new machine’s package handling. By having Festo assemble and ship a bolt-in-ready handling system, the company was able to build and commission the new machine in just four weeks.
“This machine is incredibly flexible,” said Jared Jones, Chief Operating Officer, CODI Manufacturing. “All the end user has to do is swap out the gripper head to change to the number, type, and size of bottles, cans, jars, or pouches being packed into shipping cases, select a new recipe on the HMI, and start the machine.”
The largest assemblage of Festo solutions of any Pack Expo
“Machine automation typically involves both electric and pneumatic systems as the VTUX, CODI case packer, and our new Pack Expo booth demonstrate,” said Mark Walters, Festo’s new North American Industry Segment Manager for End of Line Packaging, and the architect of Festo’s Pack Expo exhibit.
“Festo is unique among global automation suppliers in terms of the breadth and depth of its electric and pneumatic solutions. Festo’s architecture seamlessly integrates with Rockwell, Siemens, and Beckhoff so that machine builders and end users gain all the engineering, operational, and support advantages of a one-stop-shop of competitively priced solutions.” Festo invites show attendees to visit the Festo booth and meet Mark Walters.
In addition to VTUX and the CODI case packer, at the Festo booth show attendees will find:
- Festo’s next generation electric automation axes, the ELGD
- The new Festo Automation Platform (AP) of remote and decentralized I/O for backplane speed communication, compatible with EtherNet/IP, PROFINET, and EtherCAT
- New multistage vacuum generators, OVPN and OASP
- Three-axis gantry handling solutions
- The Festo Global Grip-It Team of experts showing the latest adaptive and mechanical grippers
- Simplified electric motion (SMS) actuators that are comparable to the ease-of-use and competitive cost of pneumatics
- Controlled Pneumatics – similar capabilities to electric servo control
- Pneumatic safety systems, including Common Industrial Protocol (CIP) Safety
- New AC and DC multiprotocol servo drives with new single wire compatible motors
- Fabco-Air’s latest in standard and custom inch-based pneumatic cylinders
- Festo Didactic featuring hands-on upskilling systems for the packaging industry
- A new collection of the most in-demand, competitively priced pneumatic components that are in stock and ready to ship – ISO round and square body cylinders, ultra compact cylinders, air preparation systems, and polyurethane tubing
- Process automation solutions
- Clean design solutions for food and beverages
- Compressed air quality systems
- Eight dynamic displays, including VTUX, simplified electric motion, safety, three-axis handling system, and adaptive gripping.
For more information on the advantages of working within the Festo ecosystem of less engineering overhead, fast time to market, seamless connectivity, and the industry’s widest selection of electric and pneumatic automation components, visit www.festo.com.
Festo is a leading manufacturer of pneumatic and electromechanical systems, components, and controls for process and industrial automation. For more than 50 years in the U.S., Festo Corporation has continuously elevated the state of manufacturing with innovations and optimized motion control solutions that deliver higher performing, more profitable automated manufacturing and processing equipment. Through advanced technical and industrial education, Festo Didactic Learning Systems and its partners prepare workers for current and future manufacturing technologies.