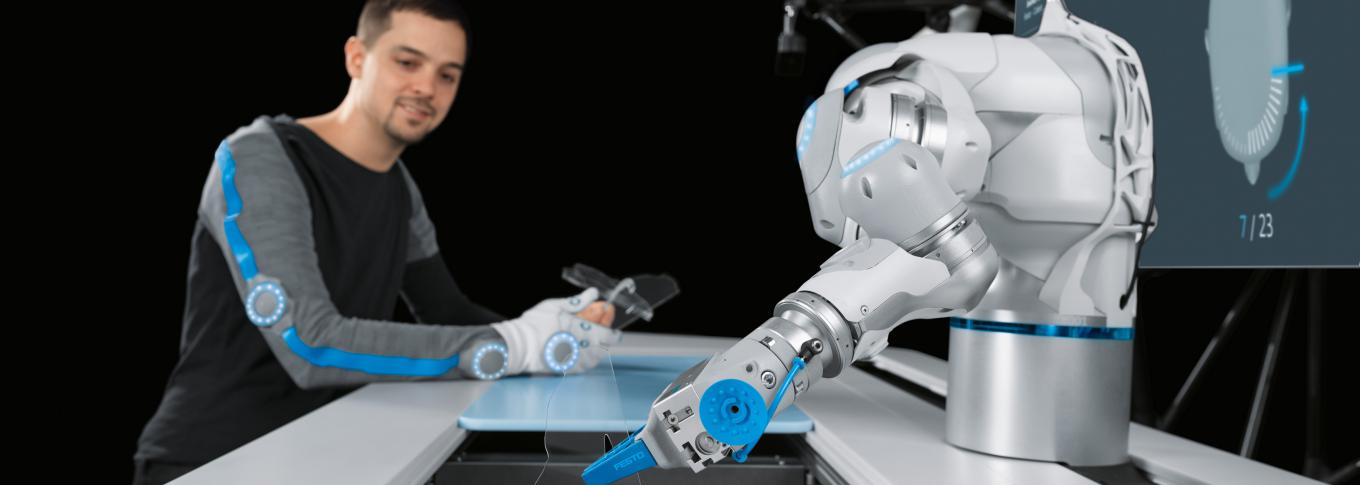
BionicWorkplace: Human-robot collaboration with artificial intelligence
Short product life cycles and a high diversity of variants are requirements brought about by industrial change. At the same time, it is becoming increasingly important to ensure that employees can rapidly and intuitively adapt to new tasks. This calls for new forms of collaboration between people, machinery and software. A key role is played here by self-learning systems with artificial intelligence and by robot-based automation solutions that can work hand in hand with the human operator and can form networks with each other. All these requirements are fulfilled by the BionicWorkplace – a ground-breaking working environment being presented by Festo.
Short product life cycles and a high diversity of variants are requirements brought about by industrial change. At the same time, it is becoming increasingly important to ensure that employees can rapidly and intuitively adapt to new tasks. This calls for new forms of collaboration between people, machinery and software. A key role is played here by self-learning systems with artificial intelligence and by robot-based automation solutions that can work hand in hand
with the human operator and can form networks with each other. All these requirements are fulfilled by the BionicWorkplace – a ground-breaking working environment being presented by Festo at the Hanover Messe 2018 trade fair.
The future of production is flexible – in terms of the products manufactured, but also of the workplace and the design of the working environment. Artificial intelligence and machine learning are transforming workplaces into learning systems that constantly develop and optimally adapt themselves to the requirements at hand. Festo is impressively demonstrating this with the BionicWorkplace, in which a human works together with a bionic robotic arm, along with numerous assistance systems and peripheral devices that are connected and communicate with each other. The operator is supported in these tasks by technology that relieves him or her of tiring or hazardous activities.
A learning system based on sensors and artificial intelligence
The entire workplace is ergonomically designed and can be individually adapted to people, right down to the lighting. Sensors and camera systems register the positions of the operator, components and tools, so that humans can intuitively control the BionicCobot by means of gestures, touch or speech. At the same time, a software system processes all the camera images and input from the various peripheral devices. It uses this information to derive the optimal program sequence. The system learns from each action initiated and thus constantly optimises itself. Controlled, programmed and set sequences therefore gradually make way for a much freer method of working.
Sharing knowledge and making it globally available
Once learnt and optimised, the processes and skills of the BionicWorkplace can be very easily transferred to other systems of the same type in real time and made available worldwide. It will be possible in future, for example, to integrate workplaces into a global network in which knowledge modules can be shared; the communication would be effected in the various national languages. Production will then become not only more flexible, but also more decentralised: the operators could call up production orders via Internet platforms, for instance, and carry them out autonomously in cooperation with the machinery – in keeping with individual customer desires and requirements. Remote manipulation of the workplace is also conceivable.
The BionicCobot as a central element
A key component of the working environment is the pneumatic lightweight “BionicCobot”. This robot is modelled on the human arm. Its movements are generated by compressed air, which makes it flexible; it can therefore directly and safely interact with people. This is made possible by digitalised pneumatics: the Festo Motion Terminal used together with the BionicCobot opens up entirely new solution spaces for safe human-robot collaboration and enables the BionicCobot to carry out either rapid and powerful, or soft and delicate movements.
Scenario for individual production
At the Hannover Messe, a scenario is being demonstrated for the manufacture of an individual product at the BionicWorkplace. To produce an individual model of a head, for example, a laser cutter first slices sections of acrylic glass: a software program converts the stored facial features of a person scanned using a smartphone into a CAD model, which it then breaks down into separate slices. The laser cutter then cuts the elements out of acrylic glass on the basis of this 3D template. The BionicCobot takes the slices directly from the cutter and gives them to the operator in the right sequence, who then assembles them to make a unique model.
The constant automatic feed of material in this scenario is ensured by a Robotino®, which autonomously travels back and forth between the stations and safely finds its way by means of a laser scanner. It is loaded by a refined version of the BionicMotionRobot, a soft robotic structure with pneumatic compartments and a 3D woven textile covering. This configuration thus combines all key elements of robot technology.
Festo is a global player and an independent family-owned company with headquarters in Esslingen am Neckar, Germany. Festo has set standards in industrial automation technology and technical education ever since its establishment, thereby making a contribution to sustainable development of the environment, the economy and society. The company supplies pneumatic and electrical automation technology to 300,000 customers of factory and process automation in over 35 industries. Digitalization, AI and the LifeTech sector with medical technology and laboratory automation are becoming increasingly important. The products and services are available in 176 countries. With about 20,600 employees in over 250 branch offices in around 60 countries worldwide, Festo achieved a turnover of around €3.45 billion in 2024. More than 8% of this turnover is invested in research and development. In this learning company, 1.5 % of turnover is invested in basic and further training. Festo Didactic SE is a leading provider of technical education and training and offers its customers worldwide comprehensive digital and physical learning solutions in the industrial environment.