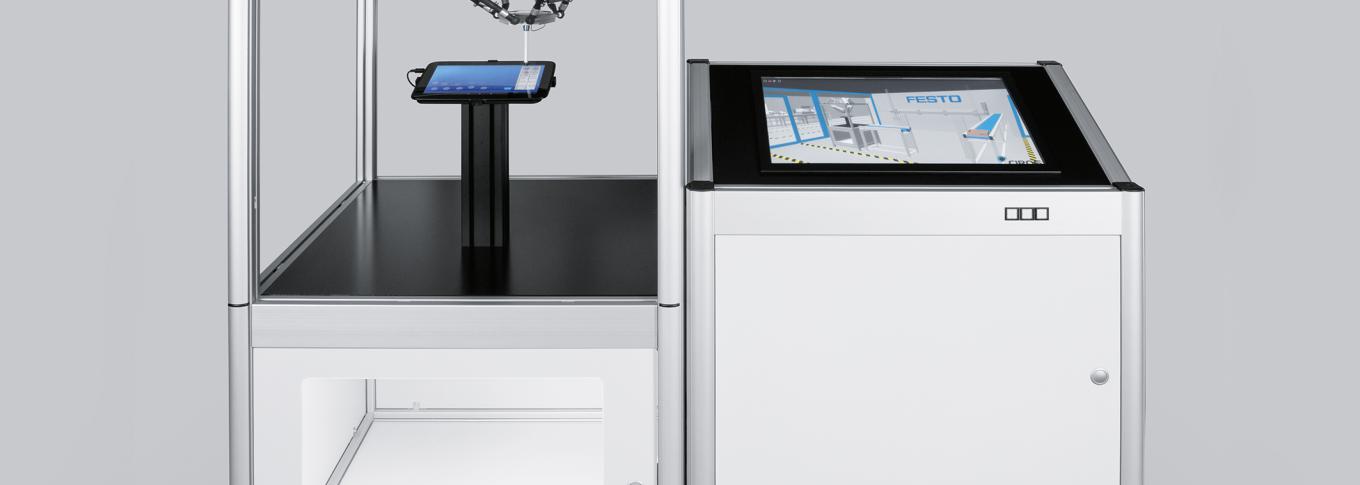
Delta robotics without control cabinet
Machines and plants with decentralised automation – this vision is coming closer to reality thanks to the CPX automation platform from Festo. The technology leader in electrical and pneumatic automation technology is now presenting a development project with delta kinematics – without a control cabinet.
Cama, an Italian packaging machine manufacturer, showcased a side loader without a control cabinet at the Interpack trade fair back in 2014, and in so doing secured a technological lead. This packaging machine featured the CPX automation platform from Festo as its controller. This opens up completely new horizons for machine and plant planners when it comes to the layout of their production lines. They now have more space and greater flexibility for integrating other plant components into the production line. (compare www.festo.com/net/en_corp/SupportPortal/Press.aspx?documentId=360348)
Controller with CPX
The development project comprising the high-speed handling system with CPX and the new “integrated drive” EMCA is now building on the trend. The delta kinematics delivering 100 picks per minute with delta kinematics permits free movement in three dimensions. The CPX automation platform integrates the entire electropneumatic control chain via a CODESYS controller: from the I/O signal and simple electrical and pneumatic movements through to transformation of the tripod models with calibration option.
The controller with CPX is revolutionary. Originally designed as a valve terminal with remote I/O, Festo is making a major leap forward with regard to decentralised automation in the machine. Thanks to IP65/67 protection, the controller and the tripod manage without a control cabinet for the first time ever.
Integrated automation with CPX
An important milestone on the road towards Industry 4.0 is the concept of integrated automation from Festo – based on the automation platform CPX. Industry 4.0 is characterised by the networking of the components within a production system, by the continuous exchange of data, by the combined evaluation of various sensor signals and by the capacity to detect complex events and critical states, up to and including independent local decision-making and control.
This electrical terminal for valve terminals already offers more than just a means of linking the field and master control levels. It already has diagnostic facilities and can provide condition monitoring functions. Its individual modules already make it possible to integrate the control of pneumatic cylinders via the modular valve terminals MPA and VTSA together with motion controllers for electric drives. And it already offers integrated safety functions.
The Internet of Things
This makes it possible to access diagnostic information, locate faults quickly and replace modules. Examples of the integration of functions include IT services such as web servers, a front end controller for decentralised local control, an end-position controller, a proportional valve or a pressure sensor for detecting internal valve terminal pressures or external signals.
CPX can already integrate all normal bus systems and Industrial Ethernet. This means that CPX is well-equipped for the future. Experts predict that the era of Industry 4.0 will mean the end of the present-day chaos of countless different bus systems. There will then be only one single, worldwide standardised protocol, an Internet protocol based on a real-time capable WLAN or Ethernet.
CPX from the Scharnhausen Technology Plant
Tens of thousands of units of the CPX are assembled according to customer requirements on spectrum test systems and assembly systems at the Scharnhausen Technology Plant every year. This requires up to 300 different components, including electronic components such as SMDs (Surface Mounted Devices) and wired components (THT – Through Hole Technology).
These components are processed on different systems using various soldering processes. Different testing methods ensure high quality. These range from automatic optical inspection (AOI) through in-circuit tests (ICT) to system tests (EOL test).
Integrated electric drive EMCA
Also crucial for the robotic system are the electric drives EMCA with integrated maintenance-free EC motors to IP54/65. The brushless DC motors with absolute position recording, integrated regulator, power electronics, absolute encoders – and the option of absolute multiturn encoders as well as integrated holding brakes and fieldbus interfaces – together with the CPX do away with the need for a control cabinet.
The electronic components of this new integrated motor are produced in electronics manufacturing at the Scharnhausen Technology Plant, with flexible manufacturing of all variants.
High-speed handling system
The handling system in the delta kinematics is characterised above all by a high dynamic response due to a low moving mass and high rigidity thanks to its pyramid-shaped, closed structure. The closed structure is created using three double rods, which ensure that the flange plate is always in a horizontal position. Axes and motors are fixed.
The delta kinematics take handling technology requirements such as short cycle times, dynamic response, function integration, fast plug and work, low acquisition and operating costs as well as faster time to market into account. The design of the tripod offers better accessibility in the working space than conventional Cartesian or Scara robots.
Virtual commissioning
The development project can be integrated into a plant as a virtual model. The first step is to create a virtual plant in a CIROS simulation. The CIROS simulation from Festo Didactic imports the tripod as a model from the CAD system and immediately processes the data further. The virtual components are then gradually replaced with real ones.
With the CIROS software from Festo Didactic, the virtual behaviour model is created and configured using the library, and serves as a simulation for the real system which is still to be produced. This means that the controller can already be developed and tested for the entire installation. This improves the quality, reduces the commissioning time and is game-changing for Industry 4.0. In the future, AML (Automation Markup Language) as the data exchange format for Industry 4.0 will become the standard for these simulations.
Equipped with virtual commissioning, OPC-UA interfaces for Industry 4.0 or the Internet of Things (IoT) and CODESYS V3 Softmotion transformation models with calibration option, the development project with CPX/EMCA is opening the door wide for Industry 4.0.
Festo es un actor global y una empresa familiar independiente con sede en Esslingen am Neckar (Alemania). Desde sus inicios, Festo ha marcado pautas en la tecnología de automatización industrial y en la formación técnica, contribuyendo así al desarrollo sostenible del medio ambiente, la economía y la sociedad. La empresa suministra tecnología de automatización neumática y eléctrica a 300.000 clientes de automatización de fábricas y procesos en más de 35 sectores. El sector LifeTech, con la tecnología médica y la automatización de laboratorios, es cada vez más importante. Los productos y servicios están disponibles en 176 países de todo el mundo. En todo el mundo, unos 20.600 empleados en cerca de 60 países con más de 250 sucursales generaron unas ventas de aproximadamente 3.650 millones de euros en 2023. De esta cantidad, alrededor del 7% se invierte anualmente en investigación y desarrollo. En la empresa de aprendizaje, las medidas de formación y desarrollo representan el 1,5% de la facturación. Festo Didactic SE es un proveedor líder de educación y formación técnica y ofrece a sus clientes de todo el mundo soluciones integrales de aprendizaje digital y físico en el entorno industrial.