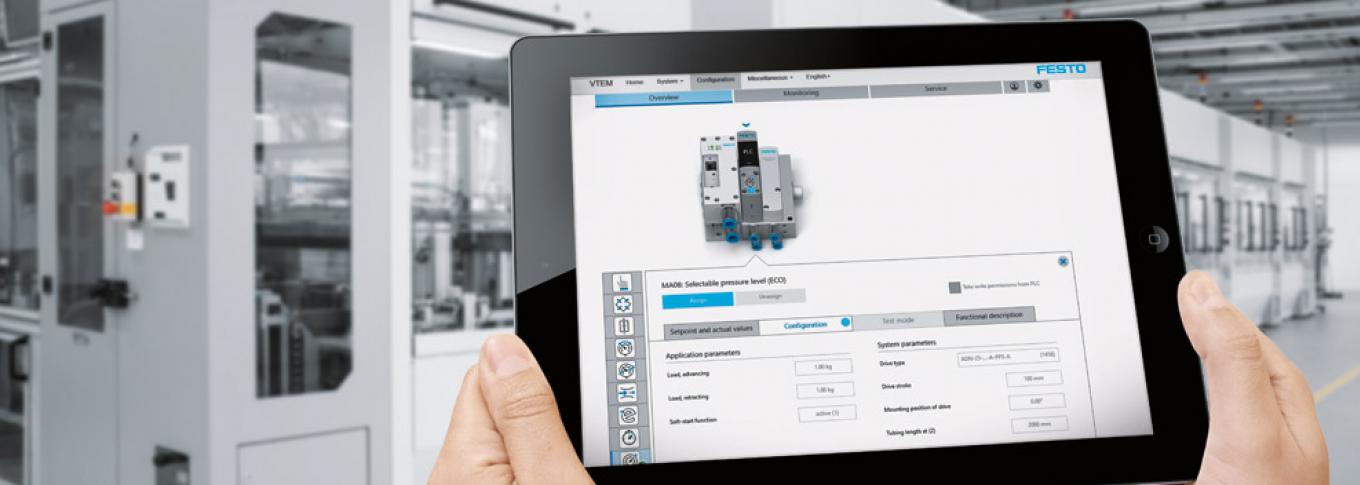
Festo makes customers ready for energy-efficient production
High energy costs, rising cost pressure and a growing awareness of climate change have turned energy efficiency into a core business objective. For many companies, having verifiable environmentally friendly and carbon neutral credentials also gives a competitive advantage. Industrial automation specialist Festo combines its Festo Energy Saving Services (FESS) with energy-saving products to help manufacturing facilities fully realise the efficiency of their compressed air system.
Modern compressed air systems are generally much more efficient than older ones that have expanded over many years. As the first company in the world to be certified by TÜV Süd for compressed air audits under the ISO 11011 standard, Festo has the necessary know-how to identify potential savings and propose and implement solutions or improvement measures.
“The air itself costs nothing. However, the electrical energy required to maintain the pressure in the system is becoming increasingly expensive. With every leakage or other malfunction, the costs increase because the more often a compressor has to start, the more energy is consumed. Therefore, optimum performance of compressed air systems saves twice: in energy costs and in CO2 emissions,” says Dr Frank Melzer, Member of the Management Board for Product and Technology Management, Festo.
In addition, the overall energy efficiency of the plant, and quality of its compressed air system also increases machine availability and thus production reliability. Depending on the size and number of audited plants, Festo estimates that up to several thousand tonnes of CO2 and energy costs in the six-digit range can be saved per year.
A new addition to the portfolio is an AI-based software solution developed by Festo that constantly monitors the compressed air system via built-in flow and pressure sensors. The measured values are recorded, processed and visualised for the operator, providing permanent condition monitoring of their system. The system reports deviations and faults in good time so that adjustments or repairs can rectify them.
For example, the VTEM digital valve terminal controls the energy supply according to demand. In addition, integrated pressure sensors can provide information on leakage conditions. This data is interpreted locally on the controller and recommends planned maintenance cycles to the operator promptly. In addition, the VTEM uses energy-saving piezo valves, which consume 20 times less energy and have a 20 times longer service life.
Another smart product is the air preparation C2M energy efficiency module, which combines pressure regulator, on-off valve, sensor technology and Fieldbus communication in one unit. It monitors compressed air consumption, shuts off the compressed air during non-production periods after a defined waiting period whilst preventing the system from falling below a defined standby pressure level.
The VSVA pulse valve is another of Festo’s newly developed, energy-efficient products. It is used for clearing chips or dust, drying and transporting parts. The pulsed air is more effective than a continuous airflow for the job and airflow saves up to 80 percent of the energy.
Festo’s OVEM vacuum generator features an integrated air-saving circuit and can monitor the vacuum pressure. Once this vacuum is reached, it switches off and automatically switches back on if the vacuum level decays. A constant vacuum pressure is not required to hold objects securely with vacuum. For smooth, non-porous surfaces, the air-saving circuit is particularly efficient and reduces air consumption by up to 60 percent.
For an energy-optimised system design, Festo also offers both a complete pneumatic and an electric portfolio with comparative calculations for both drive types. “Finding the most energy-efficient solution depends on the application” says Dr Frank Melzer. “Thanks to our pneumatic, electric and combined solutions, we can select the best and most sustainable solution for our customers in each case – this is what sets Festo apart.”
About Festo
Festo is a leading international supplier of automation technology with a turnover in 2024 of around €3.45 billion. Festo employs over 20,000 people worldwide and is a proven innovator and problem solver in pneumatic and electrical automation, where it is the performance leader. Festo offers around 36,000 pneumatic and electric products in hundreds of thousands of variants for factory and process automation technology, many of which can be tailored to specific customer needs. Sustainability, reducing its CO2 footprint, digital learning, innovation, performance and speed are the key drivers for the company's future. Festo GB operates as a carbon neutral organisation and uses the PAS 2060 standard externally audited by NQA to validate this claim to customers, employees and other stakeholders.
Festo Industrial Automation's innovative strength is demonstrated through the launch of around 100 new products every year. The company invests over 8.5% of its turnover in R&D, resulting in over 2,600 patents held worldwide. For more information about the company's products and UK / Irish services, please visit: www.festo.com/gb and www.festo.com/ie
Festo and Industry 4.0 - Festo has engaged with the Industry 4.0 initiative from its inception: as a user, manufacturer and trainer. As a member of the steering group, the company has taken an active role in defining the core standards such as the RAMI model and the Administration Shell. Festo Didactic has installed Industry 4.0 Cyber-Physical Factory training hardware systems in many leading universities and training centres. It also provides Industry 4.0 training courses for change managers and practical workshops for employees. Industry 4.0 technologies such as OPC-UA communications are embedded in the latest generation products. For more information, go to www.festo.com/digitalisation
Festo Didactic training delivers training for industry – by industry. Combining Festo's industrial heritage with its future-focused manufacturing and engineering expertise to deliver courses for greater productivity and competitiveness. Offering a wide range of open courses, structured development programmes and tailor-made, customer-specific projects on technology and Industry 4.0 and the industry-leading online training suite, Festo LX. Festo also provides state-of-the-art training equipment solutions for industrial companies and educational institutions around the world. Festo Didactic has around 56,000 education customers worldwide. More information on Festo training and consulting services can be found at: www.festo.com/didactic
Festo Bionic Learning Network encapsulates the innovative nature of Festo, raising awareness and attracting talent to the company. Exploring the links between nature and technology opens new areas of innovation and demonstrates complex ideas in a stimulating and enjoyable way. Festo works with an alliance of internal R&D, external educational establishments and specialist companies to advance bionic solutions for automation applications of the future. The objective is to benefit from bionics as a source of inspiration and to realise these in industrial automation. For more information about Festo's Bionic Learning Network, please visit: www.festo.com/bionics