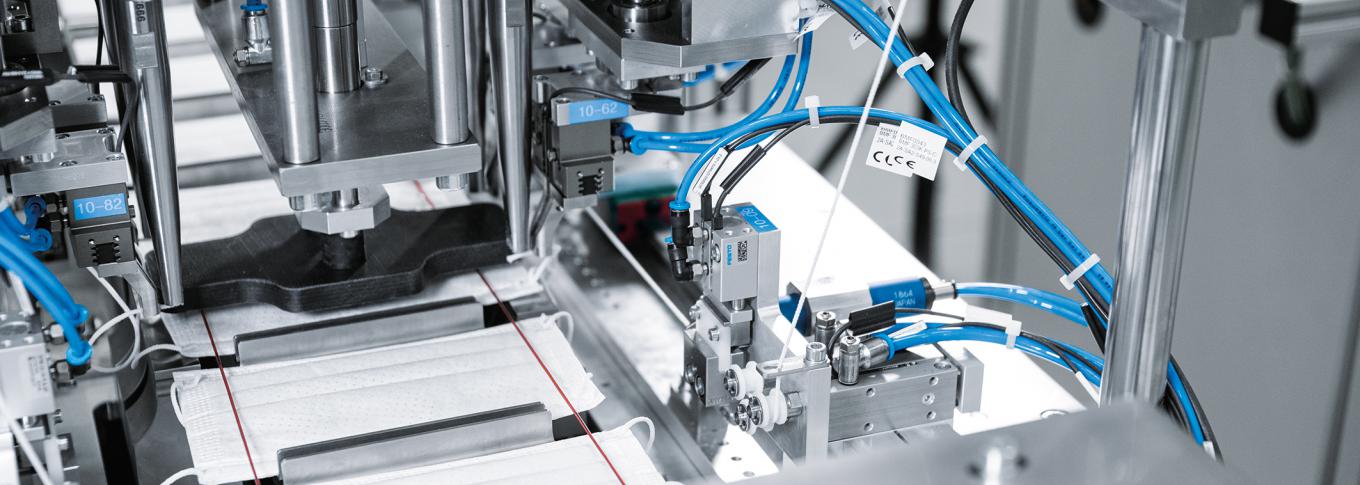
Mini factories in containers help reduce mask shortages
Protective masks are in short supply in these times of coronavirus so why not just produce some yourself?! With a system from Mikron, this is almost within everyone’s reach. This scalable system produces 50-100 face masks per minute, depending on the version. With engineering support from Festo, Mikron managed to develop the system in just six weeks.
“Normally you’d need six months for systems of this size”, explains Nils Rödel, General Manager of Mikron Berlin. But this is time you don’t have in the current coronavirus pandemic. “So 20 of our designers and fitters spent a week concentrating fully on this project and came up with a 3D model as the basis for this scalable system”, says Rödel.
Festo as a project accelerator
The project was accelerated by the engineering support provided by Festo. “Even in this period of crisis, the electric and pneumatic components we needed were available quickly. The fact that integrating and commissioning the electric drive solutions in the system as well as connecting them to the Beckhoff PLC was so quick and easy was also helpful”, says Rödel, adding: “the Festo Automation Suite software made integrating and commissioning the servo drive CMMT child’s play, and we were able to quickly make decisions about the correct sizes.”
Mini factories in containers
The beauty of Mikron’s system is that it fits in a 20-foot shipping container, which can also act as a clean room. For example in front of a hospital. Or next to a shopping centre. Or behind a school. The integrated air-conditioning system with air purification filters means that production is even possible in places with high risk of viral contamination. Depending on the raw materials, the system can operate autonomously for more than two hours. “This reduces the number of people required, and as a result the risk of infection”, explains Rödel. This means that the mini factory can also produce protective masks in remote areas or even in crisis zones where meeting hygiene standards is more challenging.
It would, in effect, be possible to produce two million protective mouth-nose masks each month with just one system. The masks are based on meltblown non-woven fabric which is made up of many layers of fine fibres, and thus filter out even the smallest particles such as bacteria and viruses from the air being breathed in. “Using official statistics, we calculated that medical personnel in Germany alone need at least 50 million protective mouth-nose masks per month”, reports Rödel. “We could meet this demand with 25 containers.”
Factory where the consumers are
Most of the time, when we talk about factories we think of huge buildings far away from where the people who need the product live. Possibly even on faraway continents, thousands of miles away from the hospitals that urgently need protective masks. This has been precisely the problem during the coronavirus pandemic: when demand skyrocketed, global supply chains were revealed to be less robust – and prone to corruption. When it comes to medical protective equipment, the failure of a delivery can cost human lives.
Eliminating the need for transport makes the end product cheaper, especially when it is possible to sell the masks to individual end consumers right where they are produced. The system, depending on how it is configured, can make packs of ten masks or individual ones, shrink-wrapped for cleanliness and in printed bags and boxes if required. “This involves docking an automated packaging station developed by our project partner pi4_robotics GmbH to the scalable system”, says Rödel.
Reliable supply of system components
Electric and pneumatic components from Festo ensure the reliable transport of the parts or perform clamping tasks in all process steps from the three-layer unwinding station, the shaping and folding station for the non-woven fabric, the ultrasonic sealing station for sealing the edges to attaching the earloops. The servo drives CMMT from Festo for controlling the electric drives EMMT are used in the application, since they can be easily connected to PLCs from other manufacturers such as Beckhoff, Siemens and Rockwell.
The pneumatic components from the Festo core product range installed in the system, such as the compact cylinder ADN, the guided drive DFM or the round cylinder DSNU are attractively priced, in stock worldwide and available within 24 hours. These are the best conditions for quickly and reliably building systems for producing masks within the shortest possible time. The pneumatic drives are actuated by MPA valves. The safety valve MS6-SV-E ensures that safety-critical system components are exhausted and de-energised as quickly as possible in the event of a sudden emergency stop.
Thanks to its international production and sales network, products from Festo are quickly available in 176 countries and enable systems to be built decentrally at locations around the world. This is entirely in keeping with the global open-source approach of the Carola project, which provided the impetus for designing the system.
Independent, decentralised and ... virtual
The system needs to be as easy to commission as it is to build. “The current travel restrictions make it extremely difficult for commissioning technicians to get to where the systems are to be built”, says Rödel. So Mikron came up with a digitised solution: “We use the HoloLens, which enables commissioning to also be done virtually using an interactive 3D projection.”
Festo is a global player and an independent family-owned company with headquarters in Esslingen am Neckar, Germany. Festo has set standards in industrial automation technology and technical education ever since its establishment, thereby making a contribution to sustainable development of the environment, the economy and society. The company supplies pneumatic and electrical automation technology to 300,000 customers of factory and process automation in over 35 industries. Digitalization, AI and the LifeTech sector with medical technology and laboratory automation are becoming increasingly important. The products and services are available in 176 countries. With about 20,600 employees in over 250 branch offices in around 60 countries worldwide, Festo achieved a turnover of around €3.45 billion in 2024. More than 8% of this turnover is invested in research and development. In this learning company, 1.5 % of turnover is invested in basic and further training. Festo Didactic SE is a leading provider of technical education and training and offers its customers worldwide comprehensive digital and physical learning solutions in the industrial environment.