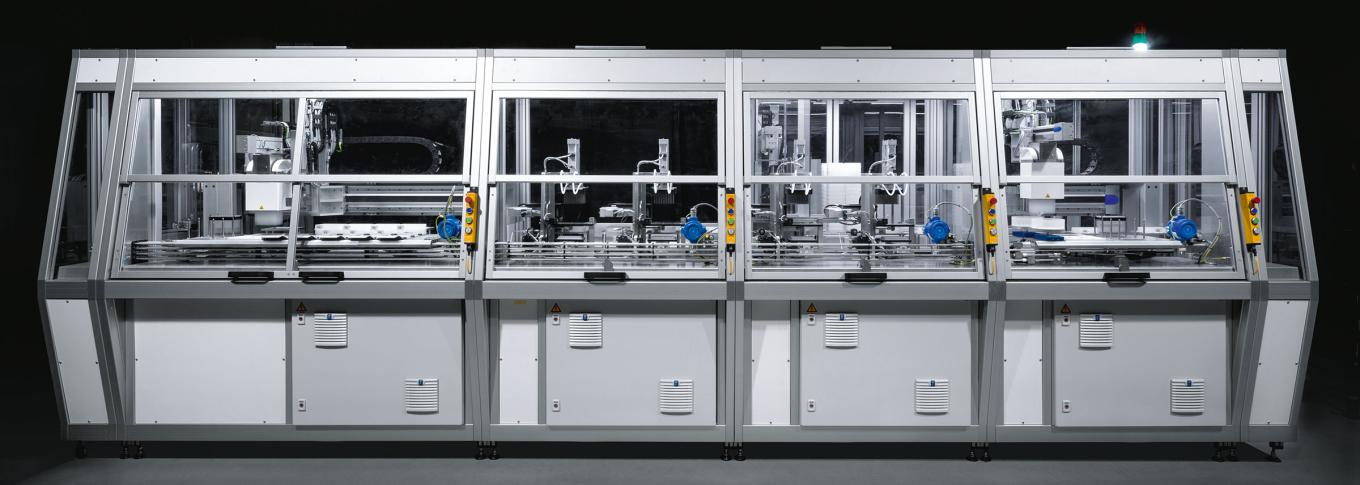
A real modular DNA factory
Seeds are the new gold. Why is that? Plant-based foods can feed an ever-growing world population. But climate change, pests and diseases threaten plant breeding. To help develop resistant seeds and make them available to agriculture, plant breeders need vast amounts of DNA. That is precisely why Synchron Lab has developed the "DNA factory", which is automated with handling gantries, electric axes, pneumatic grippers and sensors from Festo.
The system can extract a tremendous 40,000 DNA samples in the space of 24 hours. It thus meets the increasing demands for high throughput in laboratory automation. The demand for DNA samples has long been so high that it would not be possible to employ enough laboratory assistants to supply these quantities. Not to mention staffing costs. Thanks to the system, highly qualified laboratory assistants can concentrate on their core competence, the analysis of results.
High throughput: 400 microwell plates per day
Experienced laboratory assistants are able to manually extract the DNA from two microwell plates per day. With small, automated bench-top systems, a total of eight microwell plates per day can be achieved. Synchron Lab's novel "DNA factory" can manage a throughput of 400 microwell plates per day. Only one operator is needed to load and unload the microwell plates.
"Laboratories are still quite sceptical about automation. That's why it is important that laboratory staff can always see what is going on in the system," explains Glenn Dukel, Project and Business Development Manager at Synchron Lab. So they involved plant breeders in the development phase and also made the operating software as intuitive as possible, for instance using drag and drop functions.
Automated sample preparation
The system extracts DNA from shredded plant material. The process begins with a microwell plate magazine that accommodates up to 400 plates – 200 for input and 200 for output. Bar code reader SBSI from Festo scans all the microwell plates at the start of a run. Electric axes type EGC in combination with semi-rotary drive DRRD and pneumatic gripper DHPS pick up the microwell plates and place them on workpiece carriers that move from one station to the next on a transport system.
Coded metallic microspheres, so-called magnetic beads, are added to the lysate samples in the first station. The DNA attaches itself to this and can then be separated, while the rest of the material floats in the microwell plates. To do this, a buffer solution of pure isopropanol is aspirated from rotary containers with a coated silica magnet and pipetted into the microwell plates. This is how the process of DNA washing starts.
The pipetting heads are moved by a planar surface gantry EXCH along the X-axis and using an electric axis EGC-HD with the necessary rigidity along the Z-axis. Here, too, electric drives with servo motors type EMMT-AS ensure precise motion sequences. These servo motors are perfect for demanding and dynamic applications: They are characterised by very good controllability and path fidelity for positioning tasks. The space-saving one-cable plug solution reduces installation work.
Extensive washing process
The second and third stations are used for the washing process. At the second station, the binder buffer solution is aspirated. The magnet forms a ring with the buffer solution. The DNA remains in the microwell plate.
At the third station, the isopropanol buffer solution removes salts and ethanol from the DNA. Dispense head VTOI from Festo is used here. This is an efficiently controlled 8-channel dispense head for microwell plates equipped with only one valve for eight outlets. With VTOI, liquids in the smallest µl range can be dispensed and aspirated. The process is repeated four times.
The pipetting heads are moved by a planar surface gantry EXCH along the X-axis and using an electric axis EGC-HD with the necessary rigidity along the Z-axis. Here, too, electric drives with servo motors type EMMT-AS ensure precise motion sequences. These servo motors are perfect for demanding and dynamic applications: They are characterised by very good controllability and path fidelity for positioning tasks. The space-saving one-cable plug solution reduces installation work.
Automated handling modules
At the fourth station, the DNA is separated from the beads using a washout buffer solution. Four microwell plates are constantly subjected to this process at the same time, which enables the system to achieve economies of scale compared to other systems. Axes ELGC are used in the X direction and drives EGSC in the Y direction. Likewise, pneumatic grippers DHPS are used for lifting the microwell plates and semi-rotary drive DRRD for moving the plates.
"It was important for us to work on this project with an automation partner who stands for high quality and reliability as well as worldwide availability," adds Dukel. "That's why we decided on automation technology from Festo in line with the motto 'The best or nothing', as per the slogan of a renowned automotive brand."
In fact, the highly automated system has similar features to those of an automobile factory – with high productivity and modularity. Synchron Lab is therefore setting a gold standard in DNA extraction, enabling seed producers to respond to the enormous global demand in agriculture in the future.
About Synchron Lab
Synchron develops customised solutions for laboratory automation and specialises in the automated handling of liquids. Synchron is known in the industry as a progressive and innovative company. Since 1985, the company has been developing customised products thanks to the excellent relationships it has established with laboratory equipment manufacturers. Their products, both software and hardware, are now used in many laboratories throughout Europe. Synchron offers expertise in all areas of automation and has a wealth of experience in the development and marketing of flexible robot automation.
Festo es un actor global y una empresa familiar independiente con sede en Esslingen am Neckar (Alemania). Desde sus inicios, Festo ha marcado pautas en la tecnología de automatización industrial y en la formación técnica, contribuyendo así al desarrollo sostenible del medio ambiente, la economía y la sociedad. La empresa suministra tecnología de automatización neumática y eléctrica a 300.000 clientes de automatización de fábricas y procesos en más de 35 sectores. El sector LifeTech, con la tecnología médica y la automatización de laboratorios, es cada vez más importante. Los productos y servicios están disponibles en 176 países de todo el mundo. En todo el mundo, unos 20.600 empleados en cerca de 60 países con más de 250 sucursales generaron unas ventas de aproximadamente 3.450 millones de euros en 2024. De esta cantidad, más del 8% se invierte anualmente en investigación y desarrollo. En la empresa de aprendizaje, las medidas de formación y desarrollo representan el 1,5% de la facturación. Festo Didactic SE es un proveedor líder de educación y formación técnica y ofrece a sus clientes de todo el mundo soluciones integrales de aprendizaje digital y físico en el entorno industrial.