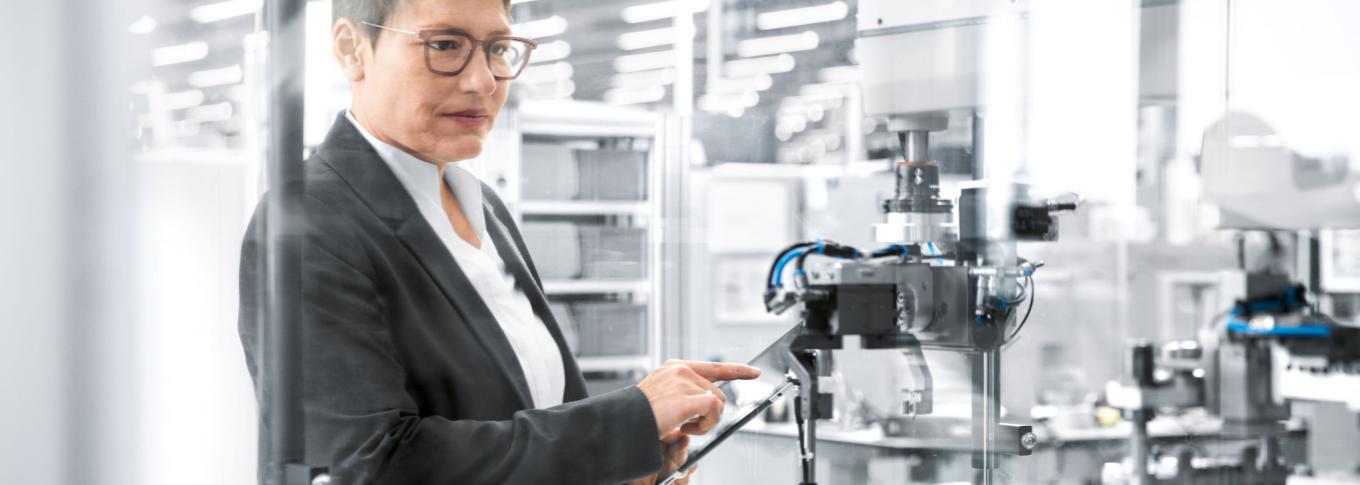
Reducing CO₂ through sustainable engineering
When it comes to reducing product-related CO₂ emissions, Festo can leverage two important aspects and also focuses on an all-encompassing approach to the CO₂ emissions caused by its products. The design of a machine lays the foundation of the CO₂ footprint at machine level. Festo supports this process first and foremost through free engineering tools. In addition, the key to a carbon-neutral future is to look at and assess CO₂ emissions from the point of view of the product, and then reduce these emissions with innovative solutions.
“Together with our customers we are actively designing the sustainable and carbon-neutral industry of the future,” explains Rebecca Sacher, Project Manager for CO₂ reduction in Sales at Festo. “The focus is always on how the customer uses our products,” adds Julia Bikidis, Project Manager for CO₂ reduction in the product portfolio at Festo. Festo supports the energy-efficient use of products right from the engineering phase. CO₂-efficient engineering revolves around two fundamental questions.
Which technology is the most efficient?
The engineering tool “CO₂ & TCO Guide” from Festo compares how much energy the various automation products consume when in operation and how this influences the total cost of ownership (TCO). Users enter the parameters of an application and the tool proposes solutions for pneumatic and electric drive technologies.
On the basis of the key deciding factors such as costs (procurement costs, energy costs, operating costs), energy consumption and CO₂ emissions per year, machine builders can decide for themselves which parameters are the most important and which drive technology they will pick.
What size is required?
Apart from deciding on the technology, a crucial factor in reducing CO₂ is sizing. “Because automation solutions are at their most efficient when they are tailored to the specific customer application,” says Sacher. The many intuitive engineering tools developed by Festo enable customers to tailor the solution to their specific application and thus reduce CO₂ emissions in the long term. Festo provides the tools “Pneumatic Sizing” and “Electric Motion Sizing” or system configurators like the “Handling Guide Online” for selecting and sizing pneumatic or electric products. These tools use evaluation matrices, cost calculators and simulations to show the users a range of clear solutions as a basis for making decisions. Needs-based sizing makes good sense, since optimally sized pneumatic drives reduce air consumption by up to 35%.
In addition to these engineering tools, the Festo Online Shop provides a filter function to allow customers to easily find sustainable products. The selected products feature energy-saving functions such as compressed air reduction or switching, which all actively contribute to reducing CO₂ emissions.
CO₂ reduction in the product portfolio starts with transparency
The principles of CO₂-efficient engineering also apply to the product portfolio. That is why Festo starts by creating transparency. “As well as looking at the CO₂ emissions in the use phase of our products, the CO₂ produced during their manufacture becomes a baseline value. We are working flat out on this calculation,” reports Bikidis. The CO₂ produced during the manufacture of Festo products depends to a large extent on the raw materials used. By using aluminium with 78% secondary aluminium (Festo Sustainability Report 2021) and implementing material reductions that are already taken into consideration in the product design, the company can reduce the CO₂ produced during manufacturing.
Digital product passport
The product carbon footprint, which includes all of a product’s CO₂ emissions, will be incorporated into the digital product passport in the future. The digital product passport will be a key tool in managing sustainability throughout the product lifecycle. “We expect the digital product passport to become the standard within the next five to ten years. We are proactively preparing for this with our activities around the digital twin based on the administration shell,” says Bikidis.
Festo is involved in various projects and associations such as the Industry 4.0 platform, in the VDMA [Mechanical Engineering Industry Association] and the ZVEI [German Electrical and Electronic Manufacturers' Association]. In the ZVEI Showcase “PCF@Control Cabinet”, for example, the company is piloting the digital twin in products like the pressure sensor SPAU.
Visionary software for energy savings
As well as the vision of Industry 4.0, Festo is also driving the vision of a carbon-neutral product portfolio. As part of this, Festo is currently working on a software program for energy-optimised pneumatic motion. This software should enable a significant energy saving of up to 70% when using pneumatic solutions, without any reduction – if not an improvement – in performance. This approach from Festo illustrates how the future of a carbon-neutral industry is becoming reality. “The biggest help to us here will be the technological advantage of Controlled Pneumatics,” emphasises Bikidis.
“By being transparent about our products’ CO₂ emissions, both in terms of how they are manufactured and used, the support we provide on the design side and our continuous pursuit of carbon-efficient product innovations, we are enabling our customers to manufacture in a carbon-neutral way,” sum up Rebecca Sacher and Julia Bikidis.
费斯托 (Festo)是一家全球性的独立的家族企业,总部位于德国埃斯林根。自成立以来,Festo在工业自动化技术和技术教育方面制定标准,从而为环境、经济和社会的可持续发展做出贡献。公司为超过35个行业的30万家工厂和过程自动化客户提供气动和电驱动自动化技术解决方案,其中生命科学和实验室自动化业务受到越来越多的关注。Festo产品和服务遍布176个国家。2024年,费斯托在全球61个国家的250多个分支机构拥有约20600名员工,实现销售额34.5亿欧元。每年约8%的销售额用于研发。在这家学习型企业,1.5%的销售额用于基础和进一步培训。Festo 教学培训 (Didactic SE) 是全球领先的技术教育和培训供应商,为全球客户提供工业环境中全面的数字化和常规学习解决方案。