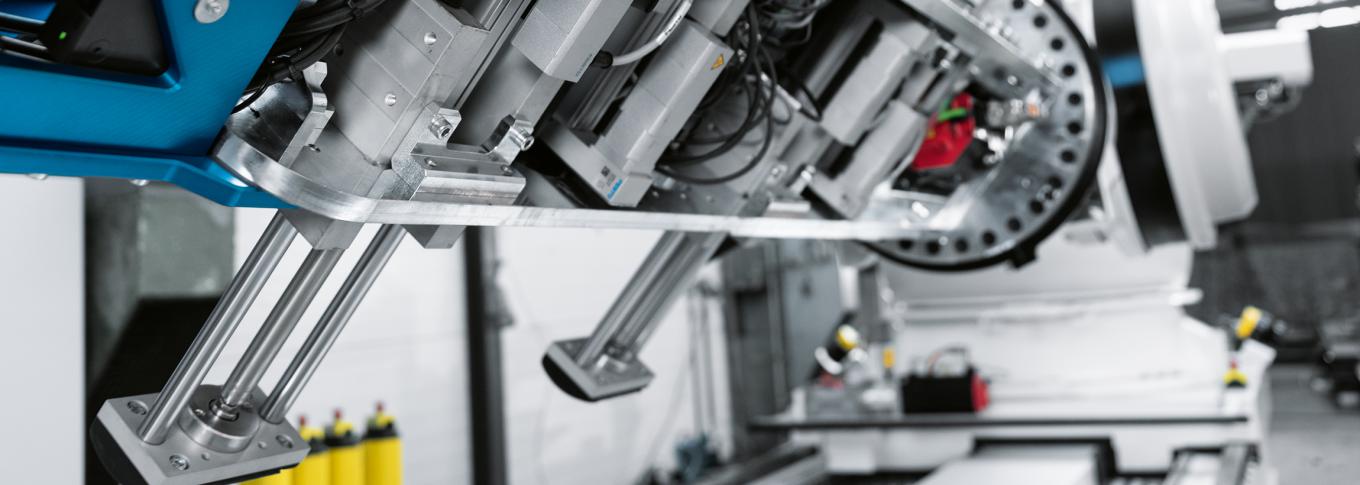
Playing it safe in the assembly of MRI machines
The future belongs to human-robot cooperation. System builder BEC developed such a collaborative solution for Siemens Healthineers. It inserts coils weighing several tonnes precisely into the magnets of magnetic resonance imaging (MRI) machines. Electric cylinders from Festo, which ensure the coils are securely gripped, play a crucial role here.
The first thing you notice when entering the BEC assembly hall is one of the world's biggest articulated arm robots with a load capacity of 2300 kg. It's like something from aerospace technology, and nothing less than high-tech. Even more eye-catching is the vast gripper system, which BEC has mounted on the robot’s articulated arm. Equipped with 3D scanners and touch-sensitive Airskin sensors, it is truly high-tech. “When the gripper picks up the coils weighing up to 1.5 tonnes and inserts them into the magnets of a future magnetic resonance imaging machine, the utmost precision is required,” emphasises Hans-Günther Nusseck, project manager at BEC.
Precise to half a millimetre
Total precision when handling objects weighing 1.5 tonnes might seem like an impossible task, but it’s all part of BEC's core competency. “It is vital that the coils do not twist or slip when the gripper picks them up and inserts them into the magnets; the tolerance for inserting the coils into the magnets is no more than 0.5 millimetres,” explains Nusseck.
This is precisely the task of four supports driven by electric cylinders EPCC from Festo. After entering the coil, the electric cylinders guide the supports against the inner wall of the coil. “The electric cylinders from Festo have proven to be the right choice. They have a compact design, but at the same time provide a large working area and thus have the necessary flexibility for 13 different coil dimensions,” says automation expert Nusseck.
Powerful and gentle at the same time
The supports need to be powerful enough to be able to hold the coils weighing up to 1.5 tonnes, but at the same time not so powerful that they damage them. “The Festo electric cylinders do an excellent job here,” emphasises Nusseck. On a practical note, the drive amplifiers, in this case the servo drives CMMT-ST, are mounted on the robot itself, rather than on the gripper system. “This frees up space on the gripper and makes it less complicated,” reports Nusseck.
Thanks to the compact ball screw drive, the electric cylinder EPCC guarantees quiet operation and precise positioning. Low internal friction ensures short positioning times and a high dynamic response. It is available in four sizes with a non-rotating piston rod, a stroke of up to 500 mm and a plain bearing guide, and includes life-time lubrication for a long service life. The integrated coupling and double bearing make for a compact design. The motor can be mounted in an axial or parallel position, and this can be changed at any time.
The servo drive CMMT-ST has a PROFINET interface for easy integration into existing control systems. “We started working with Festo right from the initial phase of the project to make sure that the drives were designed, sized and commissioned efficiently and matched the overall system,” explains Nusseck.
Free and safe movement in the workspace
Siemens Healthineers uses the system to assemble its MRI machines. It makes the process steps involved in inserting the coils into a magnet significantly safer and more efficient. The real highlight, however, is that the system’s process steps with the articulated arm robot are automated. Thanks to sensor technology with 3D scanners and touch-sensitive Airskin sensors, the system moves freely and safely in the workspace as a collaborative human-robot solution. As a result, there is no need for a safety fence. The role of people consists solely of monitoring this first step in the production of an MRI machine. The sensors in the system ensure safety.
“It is precisely this human-robot cooperation that we consider to be our USP,” explains Nusseck. He also mentions other applications in medical technology where BEC systems are used, such as in radiation therapy for the highly precise positioning of patients at the radiation source, or a robot with seats on an articulated arm that simulates riding a roller-coaster.
About BEC:
BEC is a leading specialist in human-robot cooperation for industry, medical devices and entertainment. With inventive talent and the aim of finding clever solutions, the BEC team develops technically challenging and safety-oriented robotic applications for well-known customers worldwide.
费斯托 (Festo)是一家全球性的独立的家族企业,总部位于德国埃斯林根。自成立以来,Festo在工业自动化技术和技术教育方面制定标准,从而为环境、经济和社会的可持续发展做出贡献。公司为超过35个行业的30万家工厂和过程自动化客户提供气动和电驱动自动化技术解决方案,其中生命科学和实验室自动化业务受到越来越多的关注。Festo产品和服务遍布176个国家。2024年,费斯托在全球61个国家的250多个分支机构拥有约20600名员工,实现销售额34.5亿欧元。每年约8%的销售额用于研发。在这家学习型企业,1.5%的销售额用于基础和进一步培训。Festo 教学培训 (Didactic SE) 是全球领先的技术教育和培训供应商,为全球客户提供工业环境中全面的数字化和常规学习解决方案。