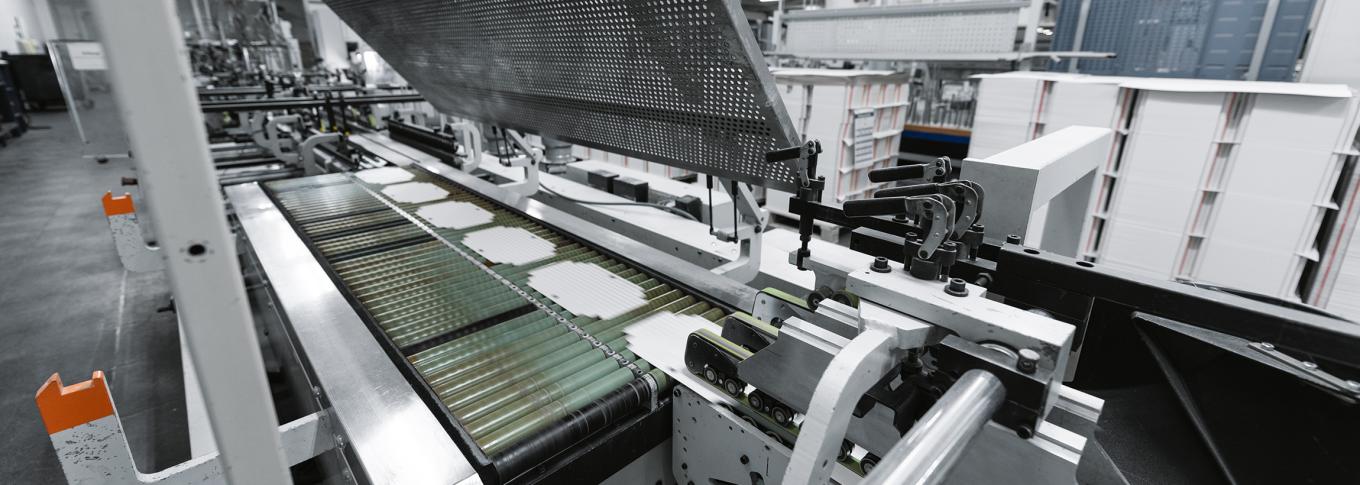
Proportional valve technology makes it possible
The sustainability of cardboard packaging is leading to its increasing use instead of plastic packaging. A key step in the manufacture of folding boxes is the highly precise gluing of the box blanks. The company Baumer hhs is a specialist and global market leader for applications of this type with its dual-piston pump DPP – supported by the proportional valve VPPM from Festo.
Folding-gluing machines process box blanks from a die cutter by folding and gluing them into finished folding boxes. Afterwards, the folding boxes are put together and filled in automatic packing machines for brand manufacturers and pharmaceutical companies. Many boxes need to be folded in and across the machine's direction of movement before the glue is applied. This ensures that the boxes can be effortlessly put together later.
Speed and precision are of the essence
Gluing machines achieve speeds of more than 700 metres per minute, and can glue well in excess of 40,000 folding boxes per hour depending on the packaging size. “So applying the right amount of glue in the right place is no easy task,” explains Marco Ahler, Technical Director at Baumer hhs.
Systems from Baumer hhs ensure that glue is applied with millimetre accuracy without any contact with the blank, even at very high production speeds. The closed system minimises cleaning and setup times. It continuously applies glue without any waste from machine standstill to maximum speed. A modular system is used in this process, consisting of a high-pressure adhesive supply, fast-switching and wear-free electromagnetic application valves and a user-friendly control unit that enables job changes at the press of a button.
Performance like an eight-cylinder
The centrepiece of this gluing process is the twin-piston pump DPP. This pump has to provide a specific pressure in order to apply the adhesive. The application of the adhesive is regulated using air pressure. The pump consists of two single-acting piston pumps, each of which take in air only on the upward stroke and displace the liquid from the glue cylinder during the downward stroke. “You could call it a two-cylinder engine with the performance of an eight-cylinder,” says Ahler, rightfully proudly.
The air pressure on the input side is converted into a largely fluctuation-free fluid pressure in accordance with the transmission ratio of the delivery pump. This enables the delivery volume to be quickly regulated and adjusted. A pressure sensor in the DPP pump measures the fluid pressure on the output side. A closed-loop pump control circuit ensures the pressure is automatically adjusted if the actual pressure deviates from the target pressure.
This is particularly advantageous when the fluid is delivered intermittently. Tests show that, when a delivery valve is opened, the spontaneous drop in the DPP pump is 25 to 50% less than with a pump with a downstream material pressure regulator, while the drop is intercepted much faster and more reliably by the closed-loop control. In addition, critical fluids are subjected to less stress and largely retain their original consistency.
Precision with proportional valve
The DPP piston pump regulates the air input pressure instead of the fluid pressure, and thus sets the required fluid pressure. The precise proportional pressure regulator VPPM from Festo controls the air volume on the input side. It has a generous linear pressure regulation range of between 0.06 and 6 bar. In the case of a delivery pump with a transmission ratio of 8:1, this means a reliable fluid pressure regulation range of 8 to 40 bar. The regulation starts with small increments to the control quality at 2 bar.
The advantage of regulating the input pressure instead of fluid pressure on the output side is that only as much compressed air is consumed as is required for the actual operating conditions. The compressed air consumption is proportional to the material pressure. As a result, the operating costs can generally be significantly reduced if the maximum delivery pressure is rarely required. For Baumer hhs, it couldn’t be clearer: “The designer of the twin-piston pump, Maren Pyttel, said to me that we could change lots of other things about the design, but the pump had to have the proportional valve from Festo,” explains Ahler.
About Baumer hhs:
Baumer hhs GmbH, Krefeld/Germany is a leading international manufacturer of industrial adhesive application systems as well as sensor-based and/or camera-based quality assurance systems. Baumer hhs offers its customers a carefully coordinated solutions portfolio for a variety of different requirements for cold glue and hot glue applications including valves, pumps and pressure vessels as well as control systems in automated production environments. The portfolio is rounded off by a comprehensive service ranging from consulting to testing innovative applications in the hhs solution centre in Krefeld to all the after-sales services. The solutions offered by Baumer hhs are used in the folding box and corrugated cardboard industry, in print processing and in special purpose machines, among others.
Festo is a global player and an independent family-owned company with headquarters in Esslingen am Neckar, Germany. Festo has set standards in industrial automation technology and technical education ever since its establishment, thereby making a contribution to sustainable development of the environment, the economy and society. The company supplies pneumatic and electrical automation technology to 300,000 customers of factory and process automation in over 35 industries. Digitalization, AI and the LifeTech sector with medical technology and laboratory automation are becoming increasingly important. The products and services are available in 176 countries. With about 20,600 employees in over 250 branch offices in around 60 countries worldwide, Festo achieved a turnover of around €3.45 billion in 2024. More than 8% of this turnover is invested in research and development. In this learning company, 1.5 % of turnover is invested in basic and further training. Festo Didactic SE is a leading provider of technical education and training and offers its customers worldwide comprehensive digital and physical learning solutions in the industrial environment.