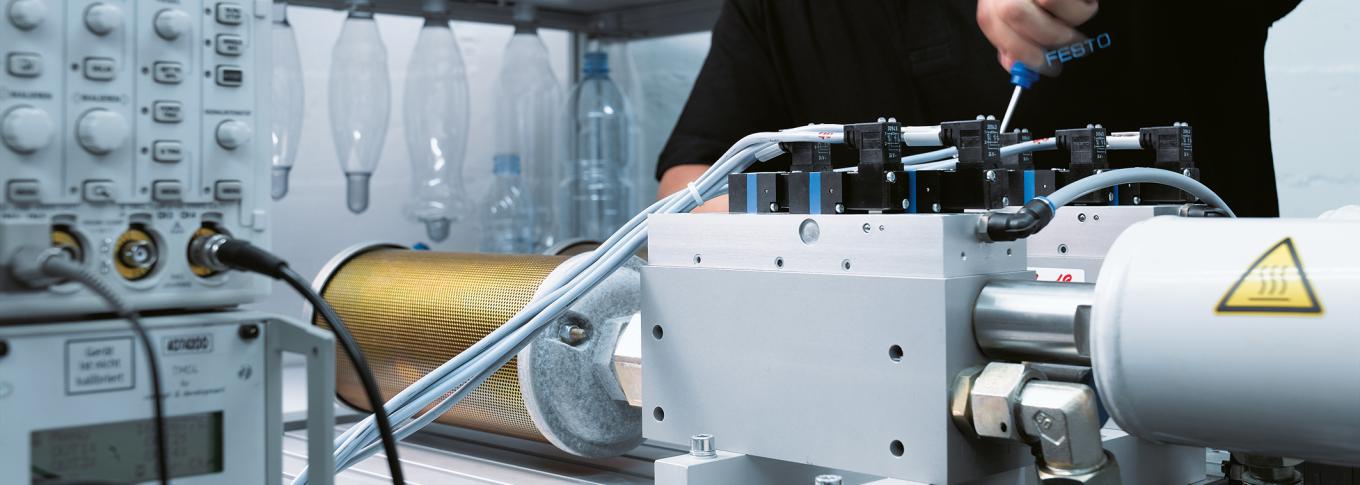
From the blank to the bottle under high pressure
Thanks to high-pressure pneumatics, stretch blow moulding machines achieve an output per blow moulding station of between 1,000 and nearly 3,000 PET bottles per hour. The key to this success is precise control using valves and valve blocks and the proper compressed air preparation. These are supplied by Festo, along with global services, from design engineering tools to operation. At drinktec in Munich in September 2022, innovative digitalisation solutions for monitoring and smart components in high-pressure applications will be on show for the first time.
For over ten years, the global player in automation technology has been developing a comprehensive range of components for high-pressure pneumatics up to 40 bar for manufacturing PET bottles using blow moulding for linear and rotary machines. The development engineers at the company’s headquarters in Esslingen use their own high-pressure laboratory where the pneumatic products are qualified. The products are manufactured and tested in the Festo Scharnhausen Technology Plant, located near Esslingen, in accordance with the Pressure Equipment Directive. You can rest assured that you get all the appropriate approvals and the quality feature “Made in Germany”.
Machine learning for monitoring
At the moment, the Festo developers are working on digitalised high-pressure applications for monitoring and other smart components. The Festo AX machine learning software plays its part, too, since it monitors and analyses machine data. It also helps to optimise production processes and save valuable resources, ensuring greater sustainability and energy efficiency.
The data collected during monitoring can be analysed via dashboards and the condition of individual valves or, depending on the scope, even entire systems can be tracked. It is not just machine conditions that can be monitored; it also makes it possible to carry out predictive maintenance.
Customised solutions for high-pressure pneumatics
The comprehensive standard range of high-pressure pneumatic products with air preparation for small to large flow rates, with modular service unit components, regulators, filters, switch-on and switch-off valves and proportional valves leaves nothing to be desired when it comes to the development of stretch blow moulding machines. In addition to the standard product range, Festo develops customised service units and valve blocks for individual machine solutions.
As a full-service provider of pneumatic and electric automation, Festo can also set the entire production line in motion, from pre-forming to palletising. Depending on the application area, Festo produces valve terminals, control cabinets, drives, control blocks, high-pressure pneumatic products or system solutions.
At the end of 2021, Festo received the “Customer Centric” award from the Sidel Group. One of the most important manufacturers of beverage filling systems thus acknowledged the tireless commitment of the Festo workers in Sales, Production, Supply Chain and Development in ensuring delivery capability.
Images and captions:
High-pressure lab:
High-pressure laboratory at Festo: here, components of high-pressure pneumatics up to 40 bar are developed for the production of PET bottles in the stretch blow moulding process for linear and rotary machines (Image: Festo SE & Co. KG))
High-pressure valve block:
Precise control for high-pressure pneumatics – with a valve block from Festo (Image: Festo SE & Co. KG)
费斯托 (Festo)是一家全球性的独立的家族企业,总部位于德国埃斯林根。自成立以来,Festo在工业自动化技术和技术教育方面制定标准,从而为环境、经济和社会的可持续发展做出贡献。公司为超过35个行业的30万家工厂和过程自动化客户提供气动和电驱动自动化技术解决方案,其中生命科学和实验室自动化业务受到越来越多的关注。Festo产品和服务遍布176个国家。2024年,费斯托在全球61个国家的250多个分支机构拥有约20600名员工,实现销售额34.5亿欧元。每年约8%的销售额用于研发。在这家学习型企业,1.5%的销售额用于基础和进一步培训。Festo 教学培训 (Didactic SE) 是全球领先的技术教育和培训供应商,为全球客户提供工业环境中全面的数字化和常规学习解决方案。