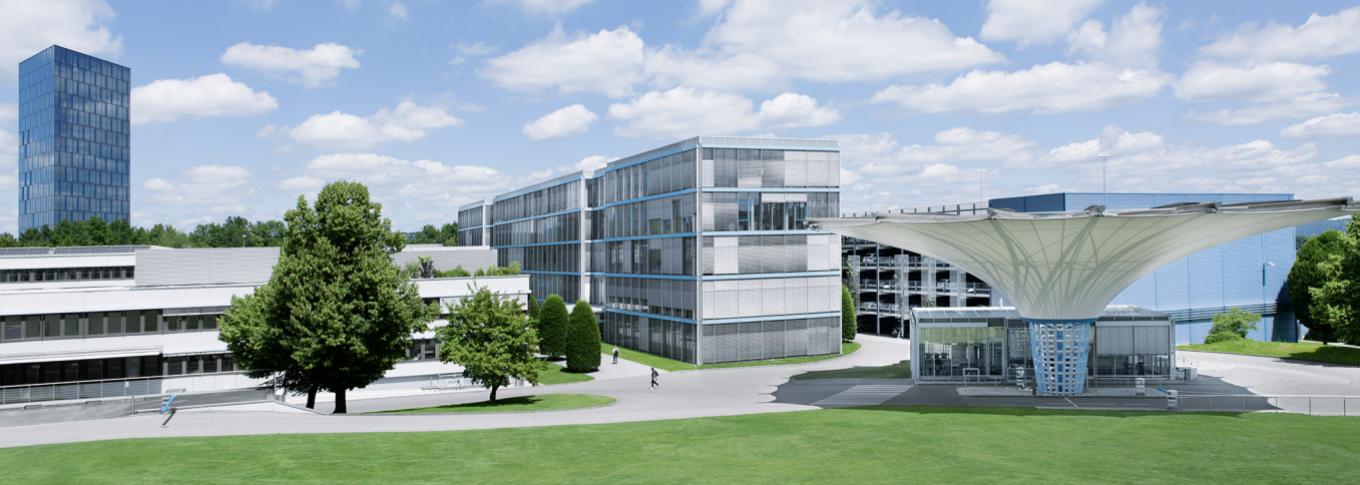
Making production adaptable
Festo’s Scharnhausen Technology Plant in the high-tech country that is Germany is at the forefront of automation for the future. The factory, where the automation company manufactures valves, valve terminals and electronics, is characterised by lean and energy-efficient processes, top-quality products and a pronounced customer focus, as well as sustainable and green production.
The overall concept was characterised by this manufacturing location’s high degree of adaptability by and the establishment of an efficient value chain and value stream. These are decisive factors for Festo’s global competitiveness and for its high level of customer benefit. “With the Technology Plant, we are also well prepared to meet future requirements: we have created the space necessary for cooperative technology and product developments there, and also considerably improved the time to market through optimised procedures and realigned core processes,” says plant manager Stefan Schwerdtle. Thanks to the new factory’s central location and its favourable infrastructure, it is ideally networked with the headquarters of Festo, with customers throughout the world and with the living environment of its employees
The value stream in a state of flux
A key attribute of the factory is its holistic value stream management. All value streams from development, logistics and production at the Technology Plant are will be constantly kept in an optimal state of flux. “We are concentrating on identifying bottlenecks in the value stream and aligning the processes accordingly in the best possible way – by this means, we can avoid delays and ensure a smooth sequence of operations,” explains Stefan Labonde, head of Material Management at the Technology Plant.
The optimisation measures for the value streams have already proved highly impressive. “In the production of the DGSL pneumatic mini slide, for instance, the overall transport distance has now been reduced from 32 km to only 240 m, and the throughput times have thus also been cut by 66% because we can now carry out all processing stages at the one location,” says Stefan Labonde.
Interdisciplinary and adaptable
When it came to planning the new plant, experts from purchasing, development, IT, logistics, production and human resources immediately got together and worked in an interdepartmental manner. In this way, it was possible to come up with intricate plant architecture and turn this into a reality in three short years. According to plant manager Stefan Schwerdtle, a dynamic adaptation in line with future requirements is one part of the concept. “The development process is by no means complete when the plant opens. We are faced with new challenges in the global competitive arena that is the automation sector with employees who are ready to learn and are open to the changes in the area of production. Also the knowledge gained from our research into Industry 4.0 is channelled into the further development of the plant. This is how we are able to implement even complex changes in a sustainable manner.”
Production site that sets an example
Besides high-performance and competitive production, the new plant also sets an example: it is used by Festo as a reference factory for its customers to demonstrate the latest automation technology and an optimal material flow and well-oiled value chain. The Technology Plant is also characterised by lean, energy-efficient processes and by highly sustainable, environmentally compatible production. This is borne out by the Platinum Certificate that was awarded to the factory by the German Sustainable Building Council (DGNB) in September 2015.
The Technology Plant in figures
The Scharnhausen Technology Plant is Festo’s main plant for the production of valves, valve terminals and electronics, and at the same time acts as a reference factory for customers. The plant occupies a total area of 66,000 square metres and employs 1,200 people. Festo has invested a total of 70 million euros in the expansion of the site.
Festo is a global player and an independent family-owned company with headquarters in Esslingen am Neckar, Germany. Festo has set standards in industrial automation technology and technical education ever since its establishment, thereby making a contribution to sustainable development of the environment, the economy and society. The company supplies pneumatic and electrical automation technology to 300,000 customers of factory and process automation in over 35 industries. Digitalization, AI and the LifeTech sector with medical technology and laboratory automation are becoming increasingly important. The products and services are available in 176 countries. With about 20,600 employees in over 250 branch offices in around 60 countries worldwide, Festo achieved a turnover of around €3.65 billion in 2023. Each year around 7% of this turnover is invested in research and development. In this learning company, 1.5 % of turnover is invested in basic and further training. Festo Didactic SE is a leading provider of technical education and training and offers its customers worldwide comprehensive digital and physical learning solutions in the industrial environment.