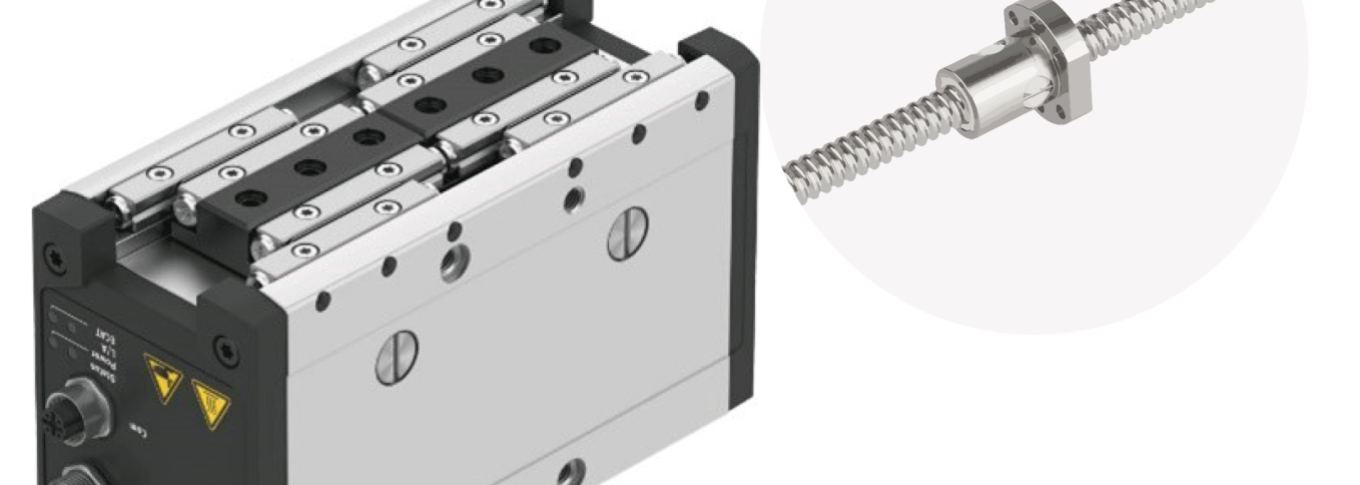
Eichenberger convinces compared to products from the Chinese market
Eichenberger successfully held its own against local Chinese manufacturers in the planning of the new Festo gripper due to outstanding quality (5000% more operational performance in the endurance test), production from a single source, years of expertise and close cooperation throughout the development process from start to finish.
„The threaded spindles from Switzerland really impressed Festo and helped the company to develop a competitive, high-performance electric parallel gripper within a very short time,“ says Dr Ralf Hartramph, Business Development Manager at Festo and former Head of Development of the Festo Technical Engineering Center in Shanghai.
New parallel gripper in shortest time
After a product range was discontinued and consequently, compatibility with the existing gripper was lost, Festo urgently needed a replacement. Therefore, Festo TEC Shanghai developed a new parallel gripper in the shortest possible time, with low manufacturing costs as an additional benefit.
In the main, the HEPP gripper was developed locally in China, where the components were sourced and manufactured. One exception was the screw drives, as these are subject to high quality standards. Only the Swiss company Eichenberger Gewinde was able to meet these requirements, and not one of the local manufacturers reached the standard.
5000% more runninge performance
„The counter-rotating spindles in the HEPP gripper from Festo are subjected to considerable stress by the feeder forces. To our surprise, the first lifetime test showed very significant differences between Eichenberger and all other spindle suppliers: the Eichenberger spindles showed almost 5000% more running performance. Not only did this convince us, but this also adds considerable value to our product,“ Hartramph explains.
The close cooperation between the development teams right from the start was another success in the rapid implementation of the project: together, Eichenberger and Festo in Shanghai developed the customised counter-rotating ball screws, so that within a few weeks the first sample screws were ready for lifetime endurance testing, which accelerated the development process enormously.
Cross-location teams
Furthermore, using multifunctional and cross-location teams together with the internally developed mechatronics, a competitive product that can withstand the most demanding requirements was created. As a result, the HEPP gripper is the first completely in-house developed electric parallel gripper from Festo, designed to be more profitable and also more compact than previous models. Festo has excelled in this respect and we are proud that our lead screws form part of this outstanding product, which is used in the automotive and electrical automation industries, among others.
Festo es un actor global y una empresa familiar independiente con sede en Esslingen am Neckar (Alemania). Desde sus inicios, Festo ha marcado pautas en la tecnología de automatización industrial y en la formación técnica, contribuyendo así al desarrollo sostenible del medio ambiente, la economía y la sociedad. La empresa suministra tecnología de automatización neumática y eléctrica a 300.000 clientes de automatización de fábricas y procesos en más de 35 sectores. El sector LifeTech, con la tecnología médica y la automatización de laboratorios, es cada vez más importante. Los productos y servicios están disponibles en 176 países de todo el mundo. En todo el mundo, unos 20.600 empleados en cerca de 60 países con más de 250 sucursales generaron unas ventas de aproximadamente 3.450 millones de euros en 2024. De esta cantidad, más del 8% se invierte anualmente en investigación y desarrollo. En la empresa de aprendizaje, las medidas de formación y desarrollo representan el 1,5% de la facturación. Festo Didactic SE es un proveedor líder de educación y formación técnica y ofrece a sus clientes de todo el mundo soluciones integrales de aprendizaje digital y físico en el entorno industrial.