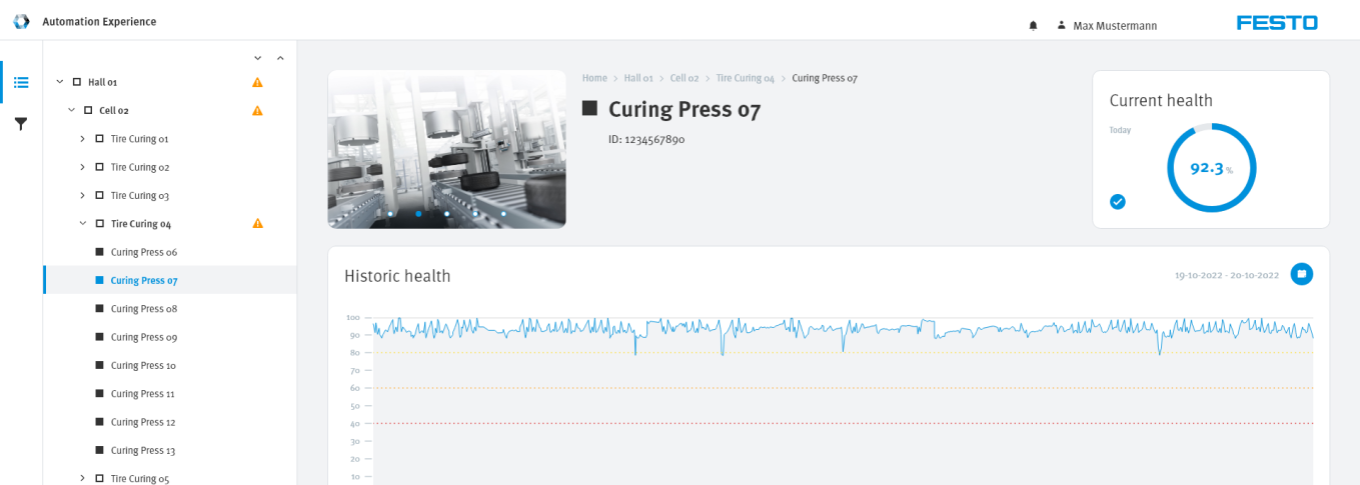
Optimising curing presses with AI
Digitalisation and artificial intelligence (AI) are megatrends that can also offer great potential for savings in tyre production. Machine learning algorithms can be implemented in a decentralised manner, for example on the edge, i.e. on the actual module to be monitored. An example is Festo AX. This AI software uses these algorithms to detect anomalies on tyre building machines or in curing presses.
Decentralised monitoring of the properties of an actuator used in the curing press, such as pressure, movement speeds and their development over time, not only enables the parameters of the actuator itself to be analysed, but also the detection of anomalies in the entire process. This is the basis for predictive maintenance concepts and for data analyses to optimise the production process. The artificial intelligence in the module control detects anomalies without additional programming effort.
Recognising problems in good time
The algorithms are taught using data from normal production and can then independently detect deviations in the production process or in the performance of the actuators. This enables plant operators to detect problems in good time and avoid unplanned plant shutdowns due to malfunctions.
In order to increase the plant availability (OEE) of a heating press, analyses showed that the generation of steam accounts for the lion's share of energy consumption and that the process valves for controlling the steam are subject to great wear. These circumstances need to be addressed, because the wear of the sealing material on the process valves means that they need to be replaced every 18-24 months in the curing presses. If a tyre factory has 200 curing presses in use, about 1500 process valves are installed. The average cost is 300 €. Extrapolated to 18-24 months, this results in costs of 450,000 €.
Avoid machine downtimes
Digitalisation solutions with artificial intelligence can detect faults before they lead to the sudden breakdown of a component. This enables maintenance staff to intervene in good time to avoid machine downtimes. One of these software solutions is the Festo Automation Experience, or Festo AX for short: "It increases the performance of machines and systems, making customers even more successful," explains Dr Oliver Niese, Head of Digital Business at Festo.
In addition to its know-how in automation technology, Festo also has domain expertise. With the acquisition of the software company Resolto, the company also has access to expertise in advanced analytics and artificial intelligence. The combination of these three parts results in the Festo AX software solution.
"Festo AX helps our customers to make decisions based on facts," emphasises digitalisation expert Niese. Festo Automation Experience (Festo AX) is an easy-to-use solution that enables users to extract maximum value from their plant data through artificial intelligence (AI) and machine learning.
Analyse data and increase productivity
Simply by analysing data with Festo AX, users can increase productivity, reduce energy costs, avoid quality losses, optimise the shop floor and create new business models. "With the Predictive Maintenance, Predictive Energy and Predictive Quality modules, we work with our customers to implement their individual solutions,” explains Niese.
Festo AX offers artificial intelligence in real time. It can be flexibly integrated into the customer's system - on premises, on edge or in the cloud. The user himself remains the owner of the collected data and no one else. Data analysis is not limited to components and modules from Festo itself. "A major advantage on the market is that our software also makes it possible to reliably analyse components from other manufacturers," emphasises digitalisation expert Niese.
费斯托 (Festo)是一家全球性的独立的家族企业,总部位于德国埃斯林根。自成立以来,Festo在工业自动化技术和技术教育方面制定标准,从而为环境、经济和社会的可持续发展做出贡献。公司为超过35个行业的30万家工厂和过程自动化客户提供气动和电驱动自动化技术解决方案,其中生命科学和实验室自动化业务受到越来越多的关注。Festo产品和服务遍布176个国家。2024年,费斯托在全球61个国家的250多个分支机构拥有约20600名员工,实现销售额34.5亿欧元。每年约8%的销售额用于研发。在这家学习型企业,1.5%的销售额用于基础和进一步培训。Festo 教学培训 (Didactic SE) 是全球领先的技术教育和培训供应商,为全球客户提供工业环境中全面的数字化和常规学习解决方案。